An In-depth Report on Perovskite & Heterojunction: New Techs and Opportunities for PV Cells
From:
Zhonglin International Group Date:06-20 1219 Belong to:Industry Related
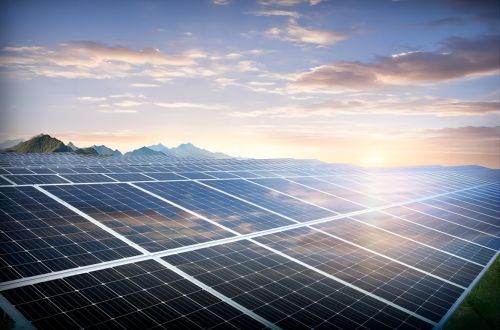
HJT, known as Heterojunction Technology, is with intrinsic amorphous layers and core structure consisting of a crystalline silicon layer and an amorphous silicon thin film. Heterogeneous PN junctions can generate higher open circuit voltage and achieve better passivation effect, making it easier to improve conversion efficiency. HJT has obvious advantages and is expected to become the mainstream of N-type: 1) It has stronger resistance to light attenuation, and can achieve power attenuation of no more than 8% in 25 years, which is significantly better than 20% of PERC and 13% of TOPCon; 2) Both sides have light transmission ability, with a double-sided rate of up to 95%, higher than PERC and TOPCon batteries; 3) Both sides have a crystal silicon+amorphous silicon structure, achieving double-sided passivation, with a passivation selectivity of up to 14.0 (only 11.7 for PERC batteries); 4) Strong adaptability, compared to double-sided PERC, the efficiency decreases less when the temperature increases, and the temperature coefficient is only -0.26%/℃ (about 0.35%/℃ for PERC, about -0.3%/℃ for TOPCon); 5) The structural stress distribution is more balanced and stable, which is easy to improve yield and reduces the subsequent operation and maintenance pressure.
The international photovoltaic Technology roadmap (ITRPV) predicts that the global HJT market share will be about 9%/13% in 2025/2030; The China Photovoltaic Association is more optimistic about the development prospects of HJT, predicting that its market share will be approximately 18%/32% in 2025/2030.
HJT signed large orders and accelerated market validation. In September 2022, Huasheng New Energy and China Electric Power Construction East China Institute officially signed a procurement cooperation framework agreement. From 2022 to 2025, Huadong Institute will purchase 10GW of heterojunction photovoltaic modules from Huasheng, which has become the largest order for N-type batteries in the industry to date and a milestone in HJT industrialization. According to CPIA prediction, the market share of HJT is expected to reach 3% in 2023, with corresponding installed capacity expected to exceed 10GW. Huasheng leads the way in expanding production. At present, Huasheng New Energy not only claims its headquarters, but also has three bases in Hefei, Wuxi, and Dali. Huasheng Xuancheng plans to have a total of 5 phases, and currently 1-3 phases have been put into operation, totaling 5GW. The 4-5 phases are expected to have equipment moved in in in June 2023 and the fourth quarter, respectively. The company achieved a sales revenue of 1.7 billion yuan in 2022, corresponding to the shipment of approximately.
MW heterojunction components. It is expected that the battery/module production capacity will reach 22.5GW/18.6GW respectively in 2023. The power of the conventional version components of Huasheng M6-144 has exceeded 500W, while the power of the conventional version components of G12-132 has exceeded 730.55W, and the conversion efficiency of the components has reached 23.5%. According to incomplete statistics disclosed by the company, the entire industry has announced that the production capacity of HJT batteries exceeds 200GW, about 8GW has been put into production, and about 53GW is under construction. It is expected that the domestic HJT production capacity will reach 68GW/97GW by the end of 2023/2025.
Compared to traditional amorphous silicon films, microcrystalline silicon films have better transmittance, lower defect density, higher doping efficiency, and higher conductivity, thus achieving higher conversion efficiency. The difficulty of microcrystalline technology lies in solving the problems of slow production pace and consistency. The basic development of single-sided microcrystals has been completed, and the challenge of double-sided microcrystals has begun. In 2022, leading enterprises and equipment manufacturers jointly completed the initial implementation of microcrystalline technology. Huasheng adopted the VHF-PECVD equipment to achieve a single sided microcrystalline HJT2.0 battery with a first chip efficiency of 24.68%. Currently, the average efficiency of the second phase of Xuancheng is about 25%, and it is expected that the average efficiency after the introduction of double-sided microcrystals this year is expected to reach 25.5%. Dongfang Risheng Double sided Microcrystalline Products; Fuxi” The pilot efficiency of the battery has reached 25.5%, and the module efficiency has reached 23.89%. Tongwei adopts the nano crystal process and is expected to achieve an efficiency of over 25.5% by the end of the year when the double-sided nano crystal import is completed. In order to achieve ultimate passivation, light absorption, and other effects, multi-layer structures developed on the basis of i-layer, a-layer, p-layer, and n-layer silicon may become mainstream, requiring higher requirements for process control
Optical conversion film or standard configuration. The silicon hydrogen bonds in HJT micro/amorphous silicon can be destroyed by ultraviolet light, leading to a decrease in power and lifespan. The traditional solution is to use a UV cut-off film to block ultraviolet light, but the absorbed light energy will be reduced. And the light conversion film can convert ultraviolet light into visible light and be absorbed by the battery, thereby increasing the power generation of the module. Empirical data shows that it can increase the module power by 1-2%. At present, leading enterprises in the industry have basically completed the import process. High water resistance materials further guarantee product life and improve long-term efficiency. In addition, the special materials and structure of HJT make it highly susceptible to moisture, and conventional packaging materials cannot meet the challenges. At present, the industry is introducing butyl rubber as HJT packaging material, and it is expected to be introduced by the end of the year.
Although the thinner the silicon wafer, the lower the short-circuit current, the HJT amorphous silicon layer can help form higher open circuit voltage, which means that the thinning of HJT silicon wafer will not significantly affect efficiency. In addition, the HJT production process is simple and uses a low-temperature environment, which is not easy to generate fragments. At present, top enterprises have achieved 110~130μ M thickness, industry is impacting 100μ The research report by TaiyangNews shows that HJT has an implementation path with a thickness of 80 microns. When the price of silicon material is 150 yuan/kg, every 10 microns reduction in silicon wafer thickness can bring a single watt silicon cost of 0A decrease of around. 01 yuan.
Half rod and half piece: After the silicon rod is square, it is divided into two half rods. Technically, the thickness of the entire piece is difficult to break through 120μ m. Half piece is easier to achieve thinness, and in May 2023, Gaoce Co., Ltd. first demonstrated the use of half piece technology to manufacture 60μ M ultra-thin silicon wafer. Edge cutting: HJT has a higher utilization rate of edge materials for silicon rods, which can improve the utilization rate of silicon rods and help reduce silicon costs by about 15%. Higher tolerance for oxygen content: HJT can use higher oxygen content tailings compared to TOPCon, which can further reduce silicon costs by about 30%.
Method 1: Optimize the grid line. It is possible to improve the printing process and refine the fine grid by combining methods such as steel plate printing; SMBB technology can be used (increase the number of main grids and reduce the width of main grids), which can not only improve the current transmission efficiency, but also directly reduce the silver consumption, and also enhance the strain capacity of the battery; The main grid (0BB) technology can be adopted, which means that the main grid does not use silver paste but directly uses conductive wires and welding strips, greatly reducing the consumption of silver paste
SMBB has become the standard process for N-type battery technology, and some leading heterojunction enterprises have achieved mass production of 18+BBs. The implementation path of 0BB technology is diverse, and the earliest and most mature one is SmartWire technology from Meyer Burger in Sweden, which has been adopted by REC; Schimid from Germany and GT from the United States also adopt similar methods. Due to patent restrictions in China, more and more adhesive welding methods are used, and we anticipate that it will still take six months to a year to achieve mature mass production and introduction.
Method 2: Silver coated copper. By adjusting the proportion of silver, copper, and additives in the slurry, performance is not reduced and silver consumption is reduced. Compared to pure silver paste, silver coated copper paste can reduce costs by 20% -50%. Silver coated copper technology has become a necessary path for HJT to reduce costs. Currently, there is no problem with the empirical data of 50% silver content, and it is breaking through the ultra-low proportion slurry below 40%. Various enterprises are gradually introducing mass production and are expected to fully use silver coated copper slurry by the end of the year.
At present, Huasheng's latest production line has achieved a single silver consumption of 100mg. The company plans to fully apply the silver coated copper+0BB technology this year, further reducing it to 70mg, equivalent to a single watt silver consumption of only 10mg or less, and reducing the cost to 0.08 yuan/W.
Method three, electroplating copper technology. Without screen printing, Cu electrode is directly electroplated and deposited on TCO, which can completely replace silver and improve conversion efficiency, with the largest space for cost reduction and efficiency increase. But at the same time, there are problems such as immature equipment, high cost, and great challenges in environmental protection approval, and the Technology roadmap has not been determined.
On August 1, 2022, Maiwei achieved a 26.41% HJT battery record by combining the electroplating copper technology of Australian metallization company SunDrive. At present, leading domestic HJT companies such as Huasheng and Tongwei have conducted demo line testing. According to calculations by Dongfang Risheng, when the electroplating copper technology can achieve an efficiency of+0.5% and a single watt cost of 0.05 yuan, it will have the ability to mass produce and import. We anticipate that the technology will require an observation period of about 2 years.
At present, perovskite used as thin film solar cell material mainly refers to organic-inorganic hybrid perovskite, which is a kind of ABX3 compound with Regular octahedron structure. Typical systems include methylamine lead iodine (MAPbI3), formamidine lead iodine (FAPbI3), etc., which are the most advanced photovoltaic materials.
The biggest advantage of perovskite lies in its high efficiency potential. In just 10 years, the laboratory efficiency has increased by 10%+to 25.8%, while crystalline silicon batteries have been used for nearly 30 years; The theoretical efficiency of a single junction perovskite battery of 33% is also greater than the limit of a crystalline silicon battery. The laboratory for perovskite/heterojunction stacked batteries has arrived at 33. 2%.
Based on the nucleation and crystallization mechanism of perovskite, polar photoenergy has been independently developed; In situ film fixation” Technology refers to the two-step vacuum solution method. Step: First, use vacuum evaporation method to form a dry skeleton, and then use solution method to react on the basis of the skeleton to form a perovskite film. The difficulties of this type of method lie in the control of skeleton morphology, solid-liquid reaction control, formula efficiency, etc. Advantages: High quality and good performance of the film layer, wide process window, easy to enlarge in large area, suitable for uneven bottom batteries, and compatible with stacked batteries.
Tongwei Co., Ltd. established a perovskite layered laboratory in 22Q2, forming a synergy with its own heterojunction and TOPCon research and development. Considering the economy of mass production, Realizability and its own process accumulation, the company chooses the perovskite/heterostructure battery route with two end stacks.
In terms of preparing calcium titanium layer, Tongwei also chose a two-step method of evaporation plating+solution, and the large-scale preparation will adopt a line source evaporation plating+narrow seam coating scheme. At present, Tongwei has completed laboratory research and development, and successfully prepared an efficient calcium titanium ore deposit with controllable skeleton, uniform coverage and no Lead(II) iodide residue.
The surface of industrial silicon wafers is rougher than that of laboratory silicon wafers, which can cause difficulties in subsequent perovskite processes and affect battery efficiency. Yaoneng Technology uses high molecular weight polymer materials as the transport layer, while achieving coating on the rough surface of the bottom battery, and then directly forms a perovskite film using a one-step wet process. This method not only simplifies the process flow, but also ensures the repeatability, stability, and efficiency of the device.
We have developed quasi planar technology in optical management. Although the trapping ability is not as good as that of a full suede structure, the biggest advantage is that it reduces process and equipment costs, and a high-performance and stable calcium titanium layer can be formed in one step. At the beginning of 2023, the company achieved a research and development efficiency of 32.44% for 1cm2 stacked batteries, which is close to the world record of 33.2%; The efficiency of the 25cm2 product reaches 30.83%, setting a world record for this size.
In May 2022, Fiberglass Optoelectronics launched the world's first commercial perovskite componentα (1.2 * 0.6m2), 5000 modules were officially shipped in July for distributed photovoltaics. In January 2023, this product passed the authoritative certification of VDE and the most important basic standards in the industry, IEC61215 and IEC61730, proving that it has the conditions to enter the market. The company is also the only enterprise in the world that has passed these certifications.
The current efficiency improvement of heterojunctions is crucial, with clear cost reduction paths and simultaneous power generation at the battery/module ends. The N-shaped screen has opened, and TOPCon has taken the lead in large-scale production; However, from the perspective of batteries, especially component products, HJT is significantly ahead of TOPCon in terms of efficiency, and has a high double-sided rate and weaker temperature attenuation, thus possessing the potential to become the next generation of photovoltaic cell technology that surpasses TOPCon. We believe that the key to current development is efficiency improvement. The efficiency difference between HJT and TOPCon, which is equivalent to the efficiency difference between TOPCon and PERC, will become an important indicator of HJT's industrialization. We expect the industry's average battery efficiency to reach 25 by the end of 2023/2024. 5%+/26%+. The efficiency improvement of the battery end relies on double-sided microcrystals, 0BB, electroplating copper, etc., while the component end relies on optical conversion film, butyl adhesive, fine reflective film, etc. In terms of cost reduction, the three main directions of thinning, silver slurry reduction, and equipment reduction are basically clarified, with a goal of achieving a silicon wafer thickness of 110&mu by the end of 2023; m. The consumption of silver slurry is 10mg/W, and the equipment is at a level of 300 million/GW.
Perovskite has outstanding advantages; Perovskite; Opening up the photovoltaic future of stacked multi junction technology. Perovskite components have advantages such as high theoretical efficiency and low material cost, and perovskite+crystalline silicon can utilize the mature crystalline silicon battery industry, perfectly connecting technological changes. This will also impact the conversion efficiency limit of 40%+or even higher for multi junction batteries based on stacking. At present, the biggest bottleneck of industrialization is large-scale preparation and stability: 1) The expansion of component area increases the preparation difficulty of core layer and functional layer, which directly leads to efficiency loss. Mass production needs to balance cost and efficiency, and propose solutions in three aspects of material formula, equipment and process. Taking core layer preparation as an example, the current Technology roadmap are diverse, and the typical two-step method of dry+wet electrooptic energy Two step dry method with infinite light energy, one step wet method with GCL Optoelectronics, etc; 2) Perovskite materials are highly susceptible to environmental impacts and are currently mainly optimized in terms of materials, structural design, and packaging processes; At present, Xianna Optoelectronics is the first to break through and has obtained VDE authoritative certification and achieved shipment. It is expected that the stability problem will gradually be solved by 2023.